From-Small-Pallet-Shop-to-Large-a-Strategic-Investment-in-Equipment-Can-Help-Relieve-Your-Labor-Sho
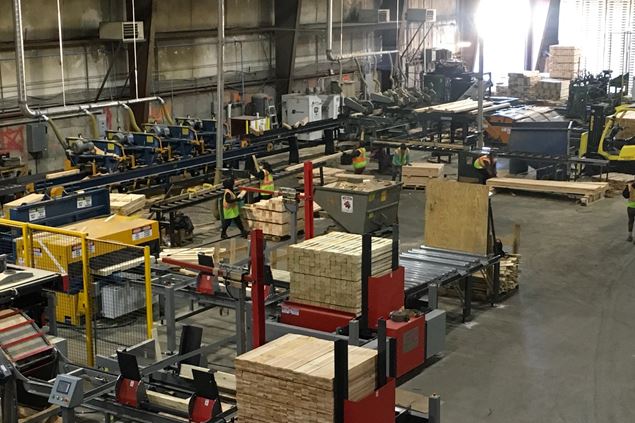
If you’ve been patiently waiting for the labor market to improve, it’s time to quit procrastinating and take action. Experts predict that finding new workers will only get harder for U.S. manufacturers over the coming years, and so it is high time to consider how investing in equipment can help lessen your dependency on employees in your production process.
According to a new report from Deloitte and the Manufacturing Institute, manufacturing job openings have been growing at double-digit rates since mid-2017, and are nearing the historical peak recorded in 2001. As many as 2.1 million manufacturing jobs will be unfilled through 2030, according to a study. The report warns the worker shortage will hurt revenue, production and could ultimately cost the US economy up to $1 trillion by 2030. Seventy-seven percent of surveyed manufacturers anticipate there will be ongoing difficulties in attracting and retaining workers in 2021 and beyond. US manufacturing executives surveyed believe that finding the right talent is now 36% harder than it was in 2018.
Pallet companies are also feeling the pinch of not having enough people. While there are various approaches available to attract and retain labor, one important area of consideration is to strategically expand investment in plant equipment. Equipment can replace the need for labor for some activities, and for others, it can make workers more productive. Whether you measure your output by pallets per labor hour or board feet per labor hour, having the right equipment can help increase productivity so that you can expand your business without adding a commensurate proportion of employees.
Here are some examples of how pallet companies can ease their dependency on employees through the strategic deployment of equipment.
Move from a cell-based manufacturing process to an in-line process
Many smaller pallet shops still rely on a variety of workstations. In new manufacturing operations, for example, stringers might be stacked, then forklifted to the notching machine, and then restacked again before being moved yet again - this time to the pallet nailing department. To stick with this analogy, by moving the notcher in line with the stringer production line, stacking and forklift requirements are reduced, resulting in labor savings.
Eliminate bottlenecks in your production process
Is there a piece of equipment in your process that is causing you to under-utilize your other machinery? For example, is your splitting capacity a constraint? By adding a high-speed thin kerf unit such as the HY400, companies can enjoy a significant boost to their lumber production operation, thus significantly increasing the number of board feet per employee. Keep in mind, however, that increasing capacity on the front end of the cut-up line means that you may find yourself with a new bottleneck on the back end, such as stacking. An investment in automated stackers can help fully optimize your line. Or if you have an automated stacker already, you might require a shift to higher capacity stackers, for example from 8 rows per minute to 25 per minute. Keep in mind that wood is half or greater of pallet cost, and your processing efficiency can be a source of competitive advantage.
What about banding wood and pallets?
People tend to accept the manual banding of lumber or finished stacks of pallets as a necessary evil. It is often performed by forklift drivers, but while they are banding, they aren’t driving. That means you are under-utilizing your forklift as well as your driver. By installing an inline automated banding machine that tedious task can be eliminated, allowing your forklift operator to be more productive.
What about other opportunities
Look around your plant for opportunities to eliminate employee touches, steps, and physical exertion. There are many mature machinery options that have not been fully leveraged by pallet shops such as automated stackers, tippers, flippers, and conveyors. Do you lose production waiting for material to arrive, or for the finished product to be removed? Infeed and outfeed conveyors can ensure that production is maintained and that the number of pallets per employee is maximized.
Consider the other employee benefits of machinery investment
Investing in machinery doesn’t just directly boost your production per employee. It can offer other benefits as well. A well-designed equipment layout can help improve consistent quality, eliminate defects, rework and waste. It can also provide a safer workplace, meaning fewer injuries to further strain employee availability. And ultimately, automation results in a more pleasant and rewarding work experience, ultimately helping to improve worker retention.
Looking ahead
Even in machinery-intensive pallet operations, there continue to be further opportunities for equipment to boost productivity. For example, design for automatic feed is an opportunity to eliminate the manual labor associated with placing boards in automated assembly lines. Likewise, scanning technologies continue to be developed that will help automate grading, improving accuracy, and reducing the need for human decision making.
In automated shops, we can look forward to getting better productivity per employee, better quality, and better working conditions. Of course, there is more to retaining a superior workforce than just equipment alone. Employee benefits, engagement strategies, second chance hire programs for ex-convicts, high school affiliation programs, and more can all play important roles in ensuring that you have the people you need to do the work. Investment in equipment, however, can make sure the people you have are as productive as possible, by eliminating the heavy lifting. Why not contact PMG to see how you can do more with less?
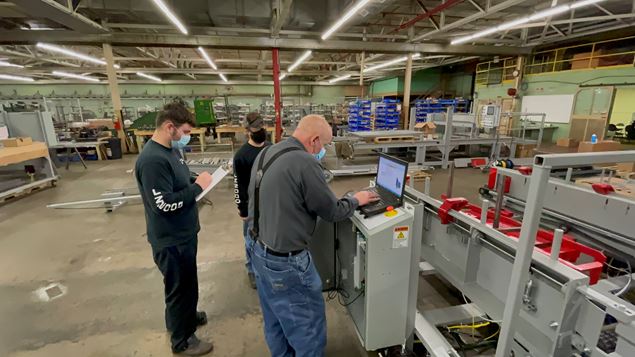
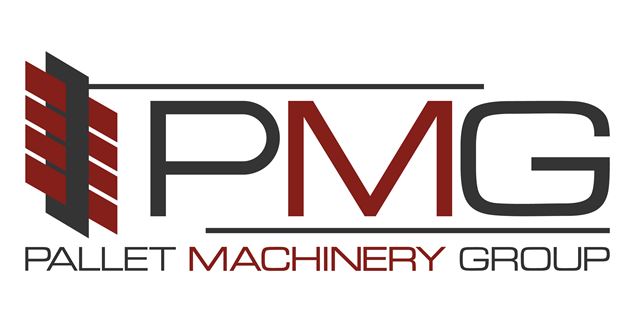