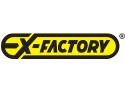
704-841-2001
Backed with a massive machinery database considered to be “the blue book” of woodworking machinery), EX-FACTORY Auctions provides a complete assessment of your equipment and allows you to interact with the market real-time in our dynamic Online Auction!
Industry
Woodworking
1860 Results Found
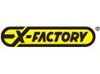
704-841-2001
Call for Price
BALEMASTER - 4550G-10: Auto-Tie Horizontal BalerSpecifications: --27"; x 40"; Opening. -- 50 HP. -- 10"; Cylinder. -- 30"; x 40"; x Variable Bale.
Call for Price
BALEMASTER - EO-650: Horizontal Auto-Tie Baler Specifications: • 25 HP Motor.• 8"; Main Cylinder.• Hopper Opening: 46";x 50";.• Bale Size: 48"; x 30"; x (variable).• Main Ram Face Pressure: 75 PSI.• System Pressure: 2,000 PSI.• Total Compression Force: 100,500 Lbs.
$14,375
Balestrini "MICRON" Slot Mortiser:Sprcifications -- Dual spindle system, (1) each side with tables and overhead holddown, 3 HP - 9,000 RPM spindles, (60 - 350) oscillations/Min, 18 mm collet dia. -- Capacity: 4-23/32" (120 mm) Max. length of slot, 3-1/8" (80 mm) max. slot depth, 1-3/16" (30 mm) max. slot thickness. - Hourly production rate of (500 - 800) slots.
$12,900
BALESTRINI MINI C 2500 DOUBLE SIDED TEMPLATE PROFILE SHAPERSpecifications: -- (2) Offset shaping heads with 10 HP (7.5 kW), 230/460 volt three phase drives. (1 each side) -- Maximum reciprocating length 98" (2500 mm). -- Maximum height 7" (180 mm). -- Maximum width between spindles 8", and shaping heads are staggered for full end rounding. -- 1¼"; Diameter work arbors with 7″ under the nut capacity, and Spindle speed of 8400 RPM -- Hydraulic stroke of 9-3/4″ wide x 110″ long tee slotted work table, with feed speeds of 3 - 49 feet per minute (1-15 m/Min.) powered by 3 HP, 230/460 volt three phase hydraulic pump -- Overhead beam clamp bar with (4) adjustable clamps. -- Push button operator control station.
$5,950
BALESTRINI - 2 CAP: MortiserAutomatically mortises or bores round holes in chairs or case good.Specifications -- Twin tables with: Pneumatic holddown clamps, (1) on each side eliminating dead cycle time; 19" long tables tilt left or right 0° to 20°.Equipped with & Features: -- 3 HP - 9,000 RPM Spindle motor and 1 HP oscillation motor. -- Spindles are mounted on prismatic guides with: Adjustable bronze gibs and move by rack & pinion. -- (120 - 240) Oscillations/Min; 4-23/32" max. oscillation length. -- 3-1/8" Max. depth; 7/8" max. bit dia.; 13 mm spindle collet dia.
BALESTRINI 2 CAP Mortiser --Automatically mortises or bores round holes in chairs or case good --Specifications -- Twin tables with pneumatic holddown clamps, (1) on each side eliminating dead cycle time, 19" long tables tilt left or right 0ø to 20ø. --Equipped with & Features -- 3 HP - 9,000 RPM Spindle motor and 1 HP oscillation motor. -- Spindles are mounted on prismatic guides with adjustable bronze gibs and move by rack & pinion, -- (120) to (240) oscillations/Min; 4-23/32" max. oscillation length, -- 3-1/8" max. depth, 7/8" max. bit dia., 13 mm spindle collet dia.
$12,150
BALESTRINI - "MICRON": Slot MortiserSpecifications -- Dual Spindle System (1) Each side with: Tables and overhead holddown; 3 HP - 9,000 RPM spindles; (60 - 350) oscillations/Min; 18 mm collet dia. -- Capacity: 4-23/32" (120 mm) Max. length of slot; 3-1/8" (80 mm) max. slot depth; 1-3/16" (30 mm) max. slot thickness.Hourly production rate: (500 - 800) Slots.
$495,000
BARKER 600 HP BOILER, BIOMASS-FIRED: -- BARKER Boiler and Fuel System built & tested in 2011 as a pilot unit. Successful testing has been completed. This surplus equipment includes the following main features: -- Combustion Temp Capability- 2,000 deg. F.; Steam Flow 24,000 lbs/hr saturated; Steam Pressure 1,500 PSI @ 600 deg. F. -- Fuel Feed rate - 3,000 Lbs/hr at 1/4" biomass (5% moisture) -- Heat Input - 7,500 btu/Lbs HHV @ 22 mmbtu/hr. -- All equipment has less than 2,500 actual operating hours since installation.EQUIPMENT MAJOR COMPONENTS: Combustor, Cyclonic combustion technology, Refractory lined Heat Recovery. Steam Generator. Rotary Drum Dryer for Fuel drying - capable of 30% moisture reduction (at the above combustion parameters) and 1.5 tons per hour (installed as used equipment).BALANCE OF PLANT FUEL FEED SYSTEM: Live-bottom bin, Bunker, Feed conveyors, Wood hog, Vibrating screen, Drag and screw conveyors. Boiler water system - feed pump, water and steam piping Emissions Control: All required bag houses (SJVUAPCD) California permitted. -- Now REDUCED PRICE from $1.5 million !!
Call for Price
BECKER VTLF 2.250 VACUUM PUMP (OIL-FREE VANE):Specifications -- (1) 6.4 kW (9 HP) Oil-less (Dry) Rotary Vane Vacuum Pump System. -- Pump has: 169 CFM Total; 338 CFM max.; 25"Hg; Heavy-Duty construction; compact design; small footprint. -- 100% Oil-less Vacuum Pump is virtually maintenance-free with: Built-in carbon vanes & built-in suction filters; vacuum regulating valve; secondary suction for additional cooling; blow off valve/silencer. -- 2-1/2" BSP x 2" NPT Nipple coupled to a TFC; 1,150 RPM motor.
Call for Price
BECKER VTLF 2.250 VACUUM PUMP (OIL-FREE VANE): -- Specifications: QTY (2) 7.5 kW (10 HP) Oil-less (Dry) Rotary Vane Vacuum Pump System; -- Pump has 169 CFM total 338 CFM max. 25"Hg; Heavy Duty construction, compact design, small footprint. -- 100% Oil-less vacuum pump is virtually maintenance-free with built-in carbon vanes & built-in suction filters, vacuum regulating valve, secondary suction for additional cooling, blow off valve/silencer; -- 2-1/2" BSP x 2" NPT nipple coupled to a TFC; 1,150 RPM motor. -- Complete Becker Pump Stack, VTLF 2.250, 10HP x 2.
BECKER KVT 3.100 3.6 Kw (5 HP) Vacuum pump:Oil-less (Dry) Rotary Vane Vacuum Pump System, rated at 69 CFM and 100 cm/Hr with max. 27"Hg; Heavy Duty construction, compact design, small foot print. -- 100% Oil-less vacuum pump is virtually maintenance-free with built-in carbon vanes & built-in suction filters, vacuum regulating valve, secondary suction for additional cooling, blow off valve/silencer. -- Complete WithInlet vacuum air filter system.
Becker VTLF 250 Vacuum Pump: 9.3 kW (12 HP) Oil-less (Dry) Rotary Vane Vacuum Pump System, 176 CFM, max. 25"Hg; Heavy Duty construction, compact design, small foot print. -- 100% Oil-less vacuum pump is virtually maintenance-free with built-in carbon vanes & built-in suction filters, vacuum regulating valve, secondary suction for additional cooling, blow off valve/silencer; 2-1/2" BSP x 2" NPT nipple coupled to a TEFC; 190-255/330/440V, 1,160 RPM motorNote (2) unit available and the price is for each
Call for Price
"BECKER" VTLF 2.250 Vacuum PumpSpecifications: -- (1) 6.4 kW (9 HP) Oil-less (Dry) Rotary Vane Vacuum Pump System; -- Pump has 169 CFM total 338 CFM max. 25"Hg; Heavy Duty construction, compact design, small footprint. -- 100% Oil-less vacuum pump is virtually maintenance-free with built-in carbon vanes & built-in suction filters, vacuum regulating valve, secondary suction for additional cooling, blowoff valve/silencer; -- 2-1/2" BSP x 2" NPT nipple coupled to a TFC; 1,150 RPM motor.
Call for Price
BELFAB RPJ26-121 Pulse Jet Dust Collector with Rotary Air Lock and Transfer Fan.Specifications: -- 15,285 CFM approx. baghouse dust collector with (121) filter bags at 10-feet long with metal cages. Total of 1,884 sq. ft of cloth area. -- Filter Cleaning: Reverse Pulse Jet (RPJ) via plant compressed air that is sequenced by diaphragm valves/solenoids/manifold thru to a Venturi that injects a burst of air pressure to dislodge the dust build up on the outside of filter bags. This is a continuous process during the operation of the dust collector. (no shut down is needed). -- Main Fan: 75 HP side-mounted blower motor. with approx 26" dia. inlet. Rated at approx 15,000 CFM @ 15" SP. -- Comes with: Main starter with control panel. -- System includes: Relay/Transfer fan, steel structure support stand, low height as waste is transferred by fan, safety ladder/platform, safety railing, and approx. 20" Rotary Air Lock. -- Housing is about 8'-5" square by about 23' high overall. Weight with structure is about 8,600 Lbs. Note: Round cone section with storage capacity of about 246 cu ft may not be included. in above height and weight. -- Available in May 2025.
BELFAB - NBM-OP3 15 Tilt Truck: Modular Dust Collection SystemPatented Modular Technology can be designed for current needs & easily upgraded as required; designed for interior use. -- Rated @ 5,000 CFM with: 10" Static pressure W.G. with: HUMMER 15 HP Blower at 1,800 RPM; 14" inlet; anti-spark steel impeller. -- (3) "NBM-OP" Filter Modules each with: (18) 7" x 60" Poly Twill cloth filter tubes; 495 sq. ft. total cloth area. -- Includes (300) Gal. waste storage cap. via: (3) Heavy-Duty plastic Tilt Trucks w/rollers; each with airtight quick coupling plate & view portPrice includes: Pre-wired magnetic starter with 5' of cable.
BENCHMARK 205-HP3 Hot Melt Adhesive ApplicatorHot Melt Adhesive Applicator with: -- Bodine adjustable speed motor. -- Bead dispensing applicator. -- Also includes an extra Bodine adjustable speed motor regulator, for fine tuned glue application.
YM-800 1 YARD 4 OR 5 TINE Orange Peel GrappleSpecifications: -- Operating Weight 2,400lbs -- Opening Width 71 1/8" -- 4 or 5 Tine in stock - Ready to ship -- Rotating -- Hanger for Extra Cost
Call for Price
--This machine is in an Auction on exfactoryauctions.com--NO RESERVE-- (2 Available) BIESSE SKIPPER 100 2-Head CNC Machining Center, with Infeed & Outfeed Tables – Seller states that machine was run (2) shifts from 2005 - 2021, then only a few hours per day since! Specifications: Flexible "Top & Bottom" Machining Center that uses an innovative panel handling system. Working Capacity: "X" Axis 3,000 mm (118.11"), "Y" Axis 1,000 mm (39.37"), Max. part thickness 60 mm (2.36"). Min. workable part size: "X" Axis 90 mm (3.54"), "Y" Axis 70 mm (2.76"), & "Z" Axis 8 mm (0.31"). Work Table: Left-hand infeed & Right-hand outfeed, Each with 20-1/2” x 66” x 35-1/2” H infeed & outfeed areas with Fixed caster-type conveyor rails. Positioning Speed: "X" Axis 120 MPM (393 FPM), "Y" Axis 90 MPM (295 FPM), "Z" Axis 30 MPM (98 FPM). Boring Units: (1) Top & (1) Bottom boring blocks, Each with: 3 kW (4 HP) Motor, Boring spindle speed 4,000 RPM, (29) Vertical spindles with (17) "X" Axis & (12) "Y" Axis, (10) Horizontal spindles with (4 + 4) "X" Axis & (1 + 1) "Y" Axis, & (1) "X" Axis Grooving saw with 3 kW (4 HP) Motor, Blade speed 5,000 RPM, & Blade diameter 150 mm (5.91"). Machining: (1) Top & (1) Bottom 3.5 kW (4-3/4 HP) Electrospindles, Each with: Variable spindle speeds 7,000 - 18,000 RPM, Right-hand/Left-hand rotation, HSK D-50 Adapters for Manual push-button quick tool change, ERC-32 Toolholders & RC-32 Collets. Operator & Machine Control: Mobile Control Console, with PC-Based Control, 18" LCD Monitor, BIESSE "WORKS" + "WINDOWS" Operating system. Pedestal & Pendant controls. Equipped with: Universal transformer, 200 - 600 V, 50/60 Cy, 3-Ph., Automatic lubrication system for guides & ways, Sound hood, 79" H Safety fence with Lock-out door, & TAPESWITCH "CONTROLMAT CKP" 24" x 72" Heavy-duty ribbed pressure-sensitive safety mat. Complete with: 7’ x 9’ x 35-1/2” H Infeed Table, with Rails & Pusher. 6-1/2’ x 8’ x 35-1/2” H Outfeed Table, with Transfer Belts. Handheld Bar Code Reader. Dust Manifold. Dimensions including Safety Fence: 307" x 184" x 98" H.
$12,950
BIESSE AKRON 245 Edgebander with Corner Rounding: Left-hand material infeed for strips & coiled edge material like PVC, ABS, veneer, and solid wood.Specifications: -- 0.4 - 8 mm (5/16") Cap. Edgebanding thickness, min. panel width 85 mm & min. length 140 mm, panel thickness 10 - 50 mm.Equipped with: -- Adjustable top pressure beam positioning. -- Automatic strip & coil feed magazine with robust shear type 3 mm PVC guillotine. -- Hot-Melt glue system (12 min. heat up time) with Teflon coated gluepot, digital thermostats with automatic kick-down when machine is in idle mode; 1" dia. glue applicator roller. -- Pressure section with (1) large dia. "non-stick" coated drive roller & (2) chrome plated idle rollers with pneumatic positioning.Workstations: -- Front & Rear End Trims (0.33 HP - 12,000 RPM motors), motors travel on (2) straight slides and pneumatic tilt 0° - 25° on horizontal plane. -- Top & Bottom Flush Trims with "Quick Change" motors (1.0 HP - 12,000 RPM motors), digital readouts for easy setup. -- 2-Motor (0.3 HP - 12,000 RPM motors) Corner rounding unit for trimming leading & trailing upper & lower edge/corners with "Fast Position" and can be used as a second Top & Bottom fine trimmer as well. -- Top & bottom Scrapers for 3 mm thick PVC banding, digitals for horizontal adjustments. -- Top & bottom Buffing (0.5 HP - 2,800 RPM motors), units tilt 0° - 30°. -- Top & bottom (2,000 Watt) Hot Air Blowers with temperature adjustment. -- Feed Speed 39 FPM, 3 HP feed drive.Complete with: -- Microprocessor for workstations & feed speed. -- Insulated sound enclosure over all trim stations with triple split dust hood, industrial lights and viewing windows. -- Extendable side panel support rail, 12 KVA - 240 Hz digital frequency inverters. - Includes: Used tooling on all workstations.
BIESSE AKRON 1330 EDGEBANDER (W/PRE-MILL & CORNER ROUNDING): -- Specifications: Computer controlled interface for workstations with servos and pneumatic positioning devices. Programmable selections for 1-touch changeover between edgebanding types and thicknesses.Top Pressure Beam with automatic adjustment from the machine control. -- Working Capacity: Edgebanding thickness, 0.4 - 5 mm capacity. Min. panel width 85 mm (3.3"); min. panel length 140 mm (5.5"); panel thickness 10 - 50 mm (0.39" - 1.96").3 HP (2.2 kW) Variable Feed Speed from 10 - 20 MPM (32 - 65 FPM).Front-End Equipped With: -- Pre-milling Unit with "Auto-set" automatic intervention, Strip & Coil Edge magazine, automatic shear type guillotine. -- Hot-Melt Glue System: Teflon coated glue pot, digital thermostats with automatic kick-down when machine is in idle mode.Pressure Section with (1) large dia. "non-stick" coated drive roller & (5) Teflon plated idle rollers with servo positioning NC controlled material thickness adjustment.Workstations: -- End Trimming Unit:NC controlled end trimming unit, 0.33 HP (0.24 kW) - 12,000 RPM motors.Motors travel on (2) straight slides and pneumatic tilt 0° - 15° on horizontal. plane -- Top & Bottom Multi- Function Flush/Bevel/Radius Trimming Unit: NC Controlled 2-motor Top & Bottom Multi- Function Flush/Bevel/Radius Trimming Unit, 0.3 HP (0.24 kW) - 12,000 RPM.Servo driven positioning of motors for different edge trimming profiles & positions. -- Corner Rounding Unit:2-motor 0.3 HP (0.24 kW) - 12,000 RPM motors for trimming leading & trailing upper & lower edge/corners with "Fast Position",Unit can be used as a second top & bottom fine trimmer as well. -- Profile Scraping Unit:Top & bottom 2 mm or 3 mm thick PVC banding, digitals for horiz. adjustments. -- Flat Scraping Unit:Top & bottom glue scraping unit. -- Buffing Unit: Top & bottom Buffing Unit, 0.5 HP (0.37 kW) - 2,800 RPM motors), units tilt 0° - 30°Operator & Machine Control: -- Biesse SMART TOUCH 7" + Windows operating system, user friendly touchscreen control panel for workstations, rotating operator control panel w/keypad and LCD readout.Graphic 7" display touch screen. High-resolution screen for defined and intuitive images and text. Integrated 4GB hard disk for filing media files and the programs back up.USB port for managing in a simple and efficient way multimedia files, programs and updates. Ethernet port for connecting the machine to the net.Complete With: -- Insulated sound enclosure over all trim stations with split dust hood, viewing windows. -- Actual Model is BIESSE AKRON 1330 A